Allgemeines
Grob gesagt bestehen Mechaniken aus einem Gehäuse, einem Schaft zur Saitenaufnahme samt Zahnrad und einem zweiten Schaft, der auf der einen Seite eine Schneckenwelle und auf der anderen einen Drehflügel beherbergt. Montiert werden Mechaniken so, dass das Zahnrad bei aufgespannter Saite gegen die Schneckenwelle gedrückt wird (das ist so 'ne Art Hebelgesetz: oben zieht's und unten drückt's). Trotz Fettschmierung hat so ein Schneckengetriebe unter der Last der mechanischen Beanspruchung zu leiden, es reibt sich aus, die Funktion wird labberiger und unpräziser, bis das Spiel so groß ist, dass das Stimmen keine Freude mehr macht. Glücklicherweise gibt's inzwischen auf dem Replacement-Markt nahezu sämtliche Bauformen, auch Replikas längst verendeter Firmen, sodass für jeden das Passende dabeisein sollte.
Mechaniken gibt es in Links- oder Rechts-Ausführungen. Als Eselsbrücke mag dienen, dass, wenn die Gitarre vor einem im Ständer steht, alle Mechanikenflügel auf der linken Seite von „Links“- Mechaniken kommen und alle Flügel auf der rechten Seite von „Rechts“-Mechaniken. Eine ganz normale Rechtshänder Strat braucht also 6-Links Mechaniken.
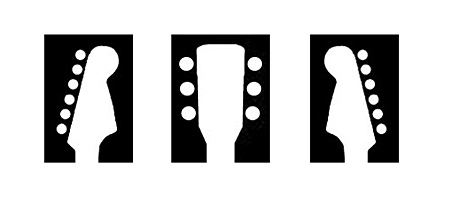
Lock-Mechaniken
Bei Lock-Mechaniken wird die Saite im Schaft festgeklemmt, dadurch entfallen die vielen Saitenumwicklungen. Das hat zum einen den Vorteil, dass beim Saitenwechsel nicht immer endlos gekurbelt werden muss und zum anderen wird eine größere Stimmstabilität erreicht, weshalb Tremolisten immer gern auf solche Mechaniken zurückgreifen. Folgende Klemmvorrichtungen sind üblich:
1. Mittels einer externen Rändelschraube wird ein Stift im Mechanikenschaft auf- und abbewegt. Dadurch wird die Saite im Schaft arretiert. Lock-Mechaniken von Kluson, Schaller und Sperzel arbeiten nach diesem Prinzip.
2. Beim Kluson Lockhead Klemmsystem wird die Saite durch das horizontale Loch im Mechanikenschaft gezogen, bis sie halbwegs straff über den Bünden liegt. Wenn man jetzt den kleinen Zylinder von oben im Uhrzeigersinn mit einer Münze (5 Euro-Cent) festdreht, wird die Saite durch einen kleinen Stift im Schaftinneren in der Querbohrung festgeklemmt.
3. Das Magnum Lock-System von Gotoh. Dabei befindet sich über dem Schaft eine Hülse, deren Innengewinde gegenläufig zur Mechanikendrehrichtung ist, d.h., nach einer Vierteldrehung klemmt der Mechanikenschaft - praktisch wie von Geisterhand - die Saite im Durchgangsloch fest und lässt sich danach wie bei einer normalen Mechanik weiterbewegen. Das lässt sich geschrieben ziemlich schlecht erklären, funktioniert aber perfekt und ist zudem auch optisch äußerst dezent.
Welche Mechaniken braucht der Mensch?
Wer sich neue Mechaniken zulegt, sollte zuerst überprüfen, ob die Mechanikenlöcher in der Kopfplatte den passenden Durchmesser haben. Je nach Bauweise der Mechaniken sind das für Gitarre 8mm oder 10mm und für Bass 12mm, 14mm oder 17mm. In kompetenten Betrieben, wie z.B. bei uns, sind die Durchmesser im Katalog und auf der Website angegeben. Um unnötiger Bastelei aus dem Wege zu gehen, sollte man sich gleich passende Mechaniken aussuchen. Aus irgendwelchen Gründen treten allerdings manchmal folgende Fälle auf:
1. Man hat z.B. einen Hals mit 10mm Bohrungen. Und den möchte man jetzt unbedingt mit Kluson-style Tunern bestücken. Deren Steckhülsen sind aber für 8mm Löcher gedacht. Kein Problem, es gibt sogenannte Adapter-Hülsen, die passen in 10mm Löcher.
2. Man hat einen z.B. Vintage-Neck, der Mechanikenlöcher von 8mm hat. Hier sollen aber unbedingt Mechaniken drauf, die 10mm benötigen. In diesem Fall sollte man den nächsten Absatz beherzigen.
Aufbohren von Mechanikenlöchern
Nicht auf den Trichter kommen, Mechanikenlöcher könnte man mit Feile und Raspel um mehrere Millimeter vergrößern. Für solches ist wirklich der begnadete und geübte Handwerker gefragt. Ansonsten hat garantiert kaum jemand als Endresultat genau in einer Linie sitzende Mechaniken. Sowas macht man mit einer Bohrmaschine, am besten mit einer Standbohrmaschine. Ein handelsüblicher Bohrständer tut's eventuell auch.
Jetzt aber um Gottes willen keinen Spiralbohrer nehmen (oder noch schlimmer: Holzbohrer mit Zentrierspitze), damit haut's einem nämlich mit Sicherheit den Hals um die Ohren. Und selbst wenn man diesen Fall ohne körperlichen Schaden übersteht, ist die einst so schöne Kopfplatte danach garantiert reif für den Sperrmüll. Nein, der gemeine Spiralbohrer ist hier wirklich nicht zu gebrauchen, Mechaniken-Bohrungen vergrößert man mit einem dreischneidigen Senker (passender Größe natürlich). Sowas gibt's natürlich auch bei uns. Kostet leider nicht wenig, aber was soll's, dieses Teil hält ewig.
Bei solchen Arbeiten bitte den Hals mit der langen Seite links vom Körper festspannen. Falls es das Ding doch mal wegreißen sollte, knallt er nämlich dann zuerst hinten gegen den Bohrständer. Leute, die manchmal erst nach dem Einschalten der Bohrmaschine feststellen, dass der Bohrfutterschlüssel noch steckte, sollten sowieso lieber gleich zum Fachmann gehen.
Nochmal: Allerhöchste Vorsicht vor Spiralbohrern größeren Durchmessers! Bitte unbedingt den Senker nehmen!!!!!!
Ganz davon abgesehen haften wir hier nicht für irgendwelche Schäden.
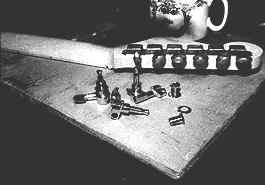
Genug gewarnt, wir schreiten zur Tat: Wir haben einen Hals mit altersschwachen Kluson-Tunern und auf den sollen neue Mechaniken drauf. Das Bild verdeutlicht die Situation.
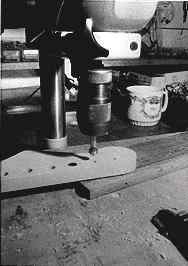
Alte Mechaniken abgebaut, eventuell zu fest sitzende Einschlaghülsen werden mit einem Werkzeug entsprechenden Durchmessers von hinten nach vorn herausgeschlagen, dann eine Bohrunterlage unter die Kopfplatte gelegt und die entsprechende Bohrtiefe ausgepeilt (ein Bohrständer mit Tiefenanschlag kann hier hilfreich sein). Noch eine kleine Raffinesse am Rande: die meisten neuartigen Gitarrenmechaniken brauchen nur auf der Unterseite eine 10mm Bohrung, oben reichen 8mm. In diesem Falle also nicht komplett auf 10mm aufsenken, sondern nur soviel, dass das Gewindestück des Mechanikengehäuses im Holz verschwinden kann. Den Senker sollte man ab und zu mal zwischkühlen, also einfach ein kleines Glas Wasser bereithalten und eintauchen.
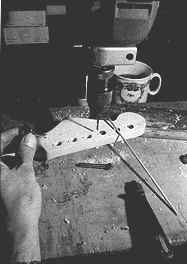
Jetzt sind da leider noch die alten Befestigungslöcher, die erfahrungsgemäß für die neuen Mechaniken nicht zu gebrauchen sind. Die müssen natürlich zugemacht werden, und zwar nicht mit Streichhölzern, sondern wie folgt: Erst werden die Löcher auf 3mm aufgebohrt (ca. 10mm, aber nicht zu tief, sonst kriegt die Kopfplatte unerwünschte Luftlöcher) und dann mit selbstgesägten Dübeln aus 3mm Holzdübelstange und Weißleim zugepfropft. Aufpassen, dass die Holzstückchen nicht zu lang sind (am besten so 8mm), sonst kriegt man sie mit dem Hämmerchen nicht ganz reingeschlagen und muss womöglich noch vorsichtig nachschleifen. Das nervt und birgt unnötige Gefahr! Also: die abgesägten Holzdübel in Weißleim tupfen und in die auf 3mm aufgebohrten Löcher drücken. Schön, wenn's gleich bündig sitzt. Überflüssiger Leim wird mit einem feuchten Lappen entfernt.
Die Montage
Jetzt werden aber endlich die neuen Mechaniken montiert. Zum Einschrauben der Gewindehülsen (Unterlegscheiben nicht vergessen) braucht man erstmal die Finger und dann, je nach Bauart, einen 10er oder 11er Schlüssel, mit dem man ganz sanft ans Werk geht. Zuerst sowieso nur ganz leicht anziehen und dann die Mechaniken ausrichten, schön parallel hintereinander. Jetzt werden die Befestigungslöcher vorgebohrt, also vielleicht erst anzeichnen, Mechaniken wieder runter und dann mit einem 2mm Bohrer vorbohren (ca. 10-12mm, je nach Schraube und Dicke der Kopfplatte). Dann wieder rauf mit den Mechaniken, die Mechanikenbefestigungsschräubchen an einem Kerzenstummel oder Stück Seife reiben und dann vorsichtig reinschrauben. Nicht zu fest, denn wenn hier der Kopf abreißt, dann aber danke. Im Zweifel nochmal im Kapitel "Schrauben" nachschlagen. Ganz zum Schluss werden die Gewindehülsen angezogen, aber auch hier bitte nicht zu fest, sonst verzieht sich das Mechanikengehäuse. Bei unserem Beispiel sieht's am Ende so aus:
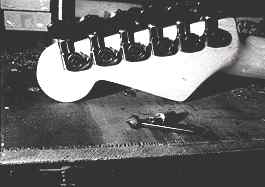
Einige Mechaniken werden nicht mit Gewindehülsen festgeschraubt, sondern erhalten Ihren Sitz durch eine Führungshülse (Einschlaghülse). Diese hat außen eine Riffelung, die dafür sorgen soll, dass die Hülse mit leichtem Druck hereingepresst schön fest sitzen soll. Diese Riffelungen haben leider nicht die absolute Maßhaltigkeit und differieren auch von Serie zu Serie. Wenn sie einen Tick zu dick sind, kann es passieren, dass beim Einschlagen das Holz reißt. Optimal ist, wenn man sie mit einem kräftigen Daumendruck hineinbekommt (notfalls mit dem Gummihammer vorsichtig nachhelfen). Hierbei darauf achten, dass die Hülse nicht verkantet. Merkt man, daß es zu schwer geht, sollte man mit einer Rundfeile den Lochdurchmesser etwas vergrößern.
Es gibt auch Mechaniken, die nur mit einer Gewindehülse festgezogen werden, z.B. Sperzel. Seitliches Drehen wird hier durch einen kleinen Stift verhindert. Am besten schraubt man solche Mechaniken gar nicht erst an, sondern richtet sie nur aus und drückt dann mit dem Daumen leicht auf die Unterseite. So markiert sich der Stift im Holz und man weiß, wo man bohren muss.
Was tun wenn...
Tja, alle Warnungen wurden in Wind geschlagen und jetzt ist von dieser kleinen, zarten Mechanikenbefestigungsschraube doch der Kopf abgedreht. Da hilft nur noch ein selbstgebautes Werkzeug. Nochmal das letzte Bild anschauen, da liegt es vorn auf dem Senker.
Im Prinzip handelt es sich um ein Metallröhrchen mit einer Innenbohrung von 3mm und einem Außendurchmesser von 5mm, also einer Wandungsstärke von 1mm. Sowas kann man sich als Rohr kaufen oder von einem Feinmechaniker aus dem Vollen drehen lassen. Danach muss man mit einer feinen Schlüsselfeile kleine Zähnchen reinfeilen. Dieses Röhrchen spannt man in die Bohrmaschine und bohrt rings um das steckengebliebene Schraubenende auf. Vorsicht, dabei entsteht brutale Hitze, also das Röhrchen immer und ganz oft zwischenkühlen (Glas Wasser).
So, nun kann das hier entstandene 5mm große Loch mit 5mm-Dübelstange ausgeleimt und dann mit einem 2mm-Bohrer neu gebohrt werden.
Die Schraube des Grauens
Bei Vintage-Mechanikenbefestigungsschrauben fängt das Gewinde nicht direkt unter dem Kopf an, sondern es befindet sich ein blanker Schaft zwischen Schraubenkopf und Gewindeansatz. Dieser Schaft hat einen größeren Durchmesser als der Kerndurchmesser des Gewindes. Hier sollte man besser 2-stufig vorbohren, einmal für den Kerndurchmesser und oben etwas größer für den Schaftdurchmesser. Bitte keinesfalls versuchen, den Schaft mit Gewalt reinzuschrauben. Das spaltet einem die Kopfplatte. Kein Witz, habe ich alles schon gesehen!